We've Got Your Back... and Knees and Shoulders! Workplace Tips for a Strong Ergonomic Process
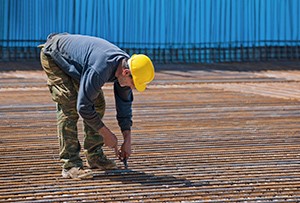
Ergonomics. We hear the term often. The Occupational Safety and Health Administration (OSHA) describes it as the process of “fitting the job to the person,” meaning using the principles of a safety and health program to address and reduce risk factors. This process can help improve productivity, reduce muscle fatigue, and lower the amount and seriousness of workplace musculoskeletal disorders (MSDs) that affect workers’ muscles, tendons, and nerves. These injuries are one of the leading causes of lost work days.
According to OSHA and the Bureau of Labor Statistics (BLS), industries with the highest rates of MSDs are construction, warehousing and transportation, health care, and retail and wholesale trade; however, employees in many other occupations can also be exposed to the ergonomic risks of heavy lifting, reaching above, bending, pulling and pushing loads, repetitive physical tasks, and laboring in awkward positions.
Developing an ergonomic process can help your workplace improve employee health and safety with the added bonus of reduced costs associated with lost work time. Below are some tips recommended by OSHA to help implement this process as well as keep it going to achieve long term wellness:
• Get managers involved. Management support is crucial for achieving results with an ergonomic process. Make sure managers are aware of the benefits of the process, and that they set and communicate program goals and assign duties throughout the workplace.
• Invite employees to participate and provide feedback. Workers often have important insights to offer. After all, they're performing their tasks daily! Involve employees in the process of identifying hazards and evaluating solutions. Encourage them to voice their questions, concerns, and ideas about making the workplace more ergonomically safe.
• Train workers. Provide employees with the information they need to understand the benefits of ergonomics. Put yourself in their position and ask yourself what you'd like to know and then communicate! Make sure crews are able to identify the hazards and related safety procedures to ensure a successful ergonomic process as you go.
• Identify specific workplace issues. Implement a process to pinpoint risks and problems unique to a facility or jobsite before they cause injuries.
• Urge employees to report signs of MSD immediately. By encouraging workers to report symptoms of MSDs as early as possible, managers can reduce the number of serious injuries and speed up the identification of safety hazards and efforts to improve them.
• Implement solutions to reduce ergonomic risks. Put into place engineering controls, safer administration and work practices, and personal protective equipment (PPE) such as ergonomic lifting and back supports, industrial ergonomic knee pads, wrist supports, wraps, and braces, and pull-on ankle supports.
• Regularly evaluate results. Establish methods for determining whether ergonomic policies are achieving the desired goals. Meet to discuss progress, correct issues, and evaluate the success of the process.
Implementing an ergonomic process can offer advantages to workplaces as diverse as offices, warehouses, construction sites, and manufacturing plants. Reduce injuries by beginning this process, involving stakeholders, and assessing progress periodically.