Protect Shipyard Employees Working Alone
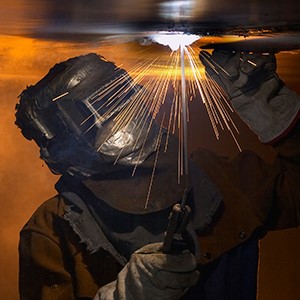
Below are some tips outlined by the Occupational Safety and Health Administration (OSHA) that will help improve the safety of employees who are working alone:
1. Know what it means to work alone. It’s important that employers, managers, and employees understand what is meant by the phrase “working alone” so the proper steps can be taken to reduce risks. Working alone refers to an employee performing a task in an isolated location or confined space. When working in an isolated area, employees work unassisted by team members due to the type, time, or location of their job. These locations might include remote areas or other work spots where employees may be unable to perform tasks near others. Confined spaces are small spaces with limited access such as cofferdams, double-bottomed tanks, or other compartments that may be hazardous due to their size.
Some examples of working alone include: one employee completing a task at the far end of a vessel, an employee working without other team members in a tank, and two employees working on opposite sides of a partition.
2. Check on workers regularly. Frequently accounting for an employee that is working alone may help reduce the severity of an injury if there is an accident. Check on workers at a frequency that is appropriate for the job being completed. While an employee working on a quick task might only need to be accounted for once, another who is working in a remote shipyard location for a full shift may need to be checked on several times to verify their safety. Also account for the worker at the completion of the task or the end of their shift, whichever may happen first.
3. Verify worker safety status by sight or verbal communication. Visual verification can be accomplished with a camera or in person. It is important that verbal communication allows both parties to speak and be heard, such as with an intercom system, two-way radios, or in-person status checks.
4. Avoid unreliable means of communication and verification. Cell phones should only be used to check on employees working in areas with consistent reception. OSHA standards do not allow cell phones to be used for verification in locations where reception cannot be demonstrated. Never rely on sounds from a whistle, power tool, or tapping on bulkheads, decks, or tank walls to verify the status of an employee.
Help reduce on-the-job injuries by providing shipyard workers performing tasks alone with thorough education and the proper safety supplies like communication systems, personal protective equipment, and confined space equipment, tools, and accessories.
Featured Products
As low as $3.29